MACHINE OVERVIEW
1. Continuous vs. Batch Operation
This has been an issue ever since large scale industrial production systems were implemented. Whether the subject is degreasing, heat treatment, vibratory surface finishing or shot blasting, etc., there has always been a demand for continuous operation. Batch operation usually requires complicated and costly handling systems for collecting parts and consolidating them into batches, loading them into the processing machine and to integrate them into the next manufacturing step. Also, batch operation frequently causes parts impingement resulting in high scrap rates.
On the other hand, continuous operation facilitates parts flow and can easily be integrated into automatic manufacturing processes saving costly handling systems and minimizing scrap rates.With its THM troughed belt shot blast machine Walther Trowal brought a continuous feed system to the market which produces results as good as any batch tumble blast machine, however, without the disadvantages of the batch machines.
2. An innovative Parts Transport System
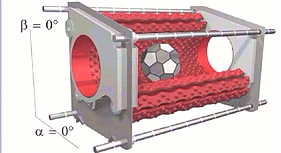
Center piece of the THM shot blast machine is the revolutionary parts transport device. The very efficient trough-feed system allows the processing of parts of all sizes, irrespective of their geometry, weight, length or fragility.
While moving forward, the parts are simultaneously rotating which insures an optimum coverage by the blast pattern from the blast wheels/turbines.
Travel speed of the parts is variable allowing blasting of the parts with just the right intensity in the optimum time frame.
The parts transport system consists of an infeed chamber, blast chamber and shakeout chamber. This makes loading of parts into the machine easy and at the same time prevents the leakage of abrasive (shot) from the THM machine.
3. Gentle Parts Transport prevents Impingement
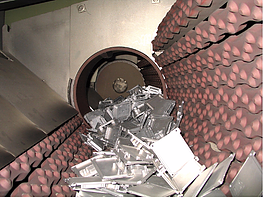
The parts are continuously fed into the THM machine and travel through the machine in the same manner. Contrary to conventional batch tumble blast machines there are practically no significant dropping heights which could cause part on part impingement. The parts transport in the THM takes place by a slow forward movement and simultaneous parts rotation. Frequently, the parts travel through the machine, one part behind the other like pearls on a string without bumping into each other with just the occasional gentle touching.
For further protection against impingement of delicate parts the tumbling mill consists of rods made from polyurethane.
This unique, gentle parts transport system allows the continuous, automatic shot blasting of delicate work pieces which in the past could only be processed with table, spinner/hanger- or wire mesh belt machines - with better results and at considerably lower cost!
4. Parts Size is no Issue
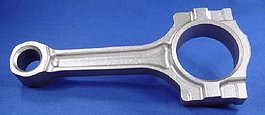
The transport system of the THM machines accommodates all kinds of parts to be shot-blasted. The THM produces perfect shot blast results for mass produced bulk parts as well as for delicate, large components with complex geometry. Parts sizes can range from 20 x 20 x 10 mm all the way up to components with dimensions of app. 1000 x 350 x 350 mm. The weight of the parts can vary from a few grams (for example small magnesium die-castings) all the way up to around 50 kg work pieces (for example heavy steel forgings) which are processed in the heavy-duty version of the THM continuous shot blast machine.
5. A truly universal Shot Blast Machine
The THM can be used for all kinds of parts. Its major applications have been in the die-casting industry for mainly aluminum and zinc die-castings. Magnesium die-castings like, for example, the housings for mobile phones or steering columns for automobiles have also successfully been processed. In the case of magnesium parts, aluminum or non-metallic abrasives like ceramic balls are used instead of metallic abrasives.
Besides for die-castings THM machines have also successfully been sold for shot-blasting of sand-castings, forged steel parts and hardened steel parts.
A very interesting application for the THM is the shot blasting (descaling) of forged aluminum parts like automotive suspension brackets which in the past had to be pickled. With the THM, the environmentally dangerous and costly pickling process could be eliminated. Moreover, the shot blasting process also generates a welcome peening effect. Of particular interest is the processing of brass components for which brass swarf from machining operations is used as abrasive. This generates an attractive mat "brassy" finish on the components.
There is practically no limit regarding parts size and shape and parts geometry. In the same machine mass produced bulk parts can as easily be processed as large, delicate components.
Besides deburring, descaling and general parts cleaning THM systems can also be utilized for shot peening. For special applications like blasting of turbine blades after machining the blasting wheels can be replaced with a compressed air blast system thus allowing the use of aluminum oxide as blasting media.
6. High capacity at low cost
THM troughed belt shot-blast machines are extremely productive with an amazingly high throughput. But productivity is not the whole story: The shot blast quality is excellent and exceeds the quality of batch tumble blast and spinner-hanger machines. And all this with a lot less energy required for the blast wheels/turbines.
Reason for the excellent shot blast results and the relatively low usage of energy is the short distance between turbines and parts. This permits the optimum use of the blasting energy with very little loss of energy compared to other types of shot-blast machine. To achieve a similar throughput a spinner-hanger machine, for example, would require 50 – 80 % more energy than the THM.
A THM 500 (tunnel diameter 500 mm) can easily process 4 – 6 Euro bins of aluminum or zinc die-castings per hour. The heavy-duty THM 700S can process up to 10 tons of forged parts with a piece weight of up to 50 kg.
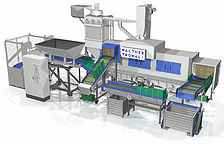
7. Parts handling
Walther Trowal offers a wide range of handling equipment for automatic loading and unloading of parts. There are hydraulic lift and tip systems, vibratory buffers, special conveyor belts for loading, unloading and intermediate storage, rotary buffer tables, etc.
8. Ease of maintenance
Shot blast machines suffer rapid wear of certain parts which must be replaced frequently. Quick access to these parts and their quick replacement is, therefore, of great importance.
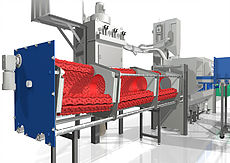
For this reason Walther Trowal engineers put a special feature into the design of the THM: The parts transport system can be pulled out of the machine housing – either by hand or on the heavy-duty THM 700 with a power winch. This allows easy access to all critical machine areas. Maintenance and parts replacement which may take 2 days in a conventional shot blast machine can be accomplished in a few hours in a THM troughed belt machine
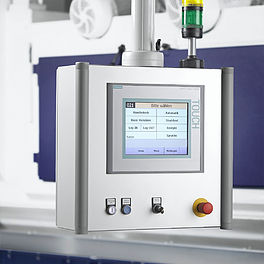
9. Electrical Panel and controls
Walther Trowal controls are developed, constructed and produced in accordance with the EC directives.